.jpg?width=300&name=waste%20water%20treatment%20(8).jpg)
Cast Iron Multistage Centrifugal Pumps
Our Cast Iron Centrifugal Multistage Pumps are engineered for applications requiring high pressure (up to 280m) and low flow rates. Ideal for tasks such as boiler feeding, firefighting systems, autoclaves, water supply systems, irrigation, and washing plants, these pumps deliver the reliable performance needed whenever high pressures are essential.
<280 metres
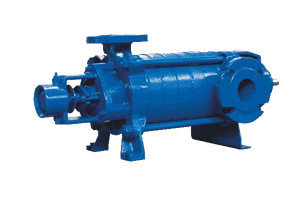
Designed for ease of maintenance, ball bearings and mechanical seals can be replaced without disassembling the main components (shaft, impellers, diffusers, and pump casings). Available with discharge sizes from DN 32 to DN 50, the TS 31-32 range comes with a mechanical seal, while the TS 40-50 range offers both mechanical seals and gland packing, with cooling chambers provided as standard.
These multistage centrifugal pumps are equipped with closed impellers and are suitable for handling clean or slightly contaminated liquids. Whether you're pumping hydrocarbons, providing water supply, or supporting industrial processes, our TS pumps are the ideal choice for reliable, high-pressure performance.
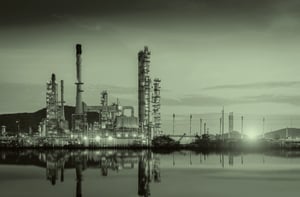
THE CREST PUMPS LIFETIME GUARANTEE
No matter how old your pump becomes, in the unlikely scenario that you have a problem, our engineers will be on hand to diagnose the issue and help you get up and running again.That’s why, with Crest Pumps you’ll never need to worry about unplanned downtime again.
Talk to us now to discuss your chemical pump requirements or book a free site audit to see how much time and money you could save!
How much are your pumps REALLY costing you?
Try our Life Cycle Cost calculator to help work out how much you could save... Upfront prices are just the beginning — energy and maintenance make up most of a pump’s lifetime cost. Our LCC calculator breaks it down, helping you compare different pump types and manufacturers to find the best solution for your needs.
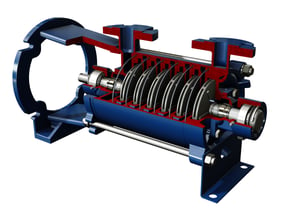
Frequently Asked Questions
Multistage pumps are centrifugal pumps (often vertically mounted) consisting of a series of impellers and casings mounted one after the other in series so that the discharge of one casing enters directly into the suction of the next. As each stage will only elevate the pressure by a set amount, a multistage pump will increase the pressure in each stage so that a final high pressure comes from the last stage.
For instance, let's take an example of a 10-stage vertical pump, and each stage can increase the pressure by 0.5 bar. Liquid enters the first stage at atmospheric pressure and is elevated by 0.5 bar to enter the second stage, this then increased the pressure by 0.5 bar to enter the third stage a 1 bar. This is repeated until the liquid exits the final stage at 5 bar pressure.
It's important to realise that only the pressure is increased and not the flow rate as the stages is mounted in series. To increase the flow rate, you would need to mount the pumps in parallel.
Trusted By The Best
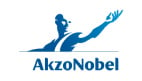
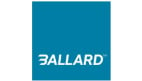
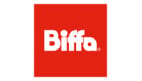
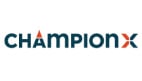
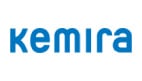

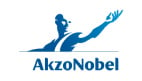
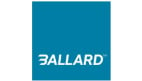
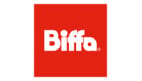
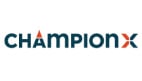
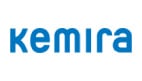

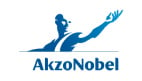
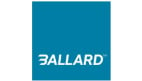
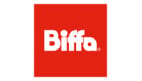
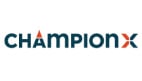
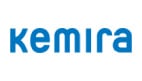

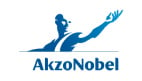
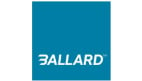
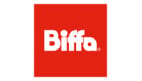
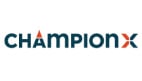
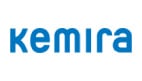

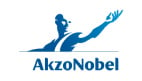
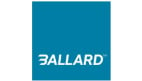
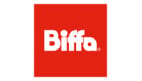
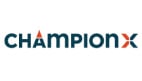
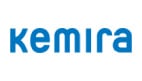

.jpg?width=300&name=waste%20water%20treatment%20(8).jpg)
DON’T JUST TAKE OUR WORD FOR IT
Crest answer our questions promptly, and always help us out when we need to source items quickly!